Como criar impressões 3D transparentes!
Talvez você já tenha tido vontade de imprimir algo transparente. No entanto, impressões 3D nesse tipo de filamento tipicamente saem numa cor branco-leitosa, ao invés de transparente. O material do filamento refrata bastante a luz, então, mesmo ela passando pelo material, ainda é refletida várias vezes no seu interior e os raios se espalham, o que cria essa aparência translúcida, mas longe de ser transparente. A ColorFab tem, em sua página um artigo onde eles mostram impressões notavelmente transparentes. Fizemos algumas impressões, e escrevemos este artigo para te mostrar como você pode fazer essas impressões você mesmo(a)!
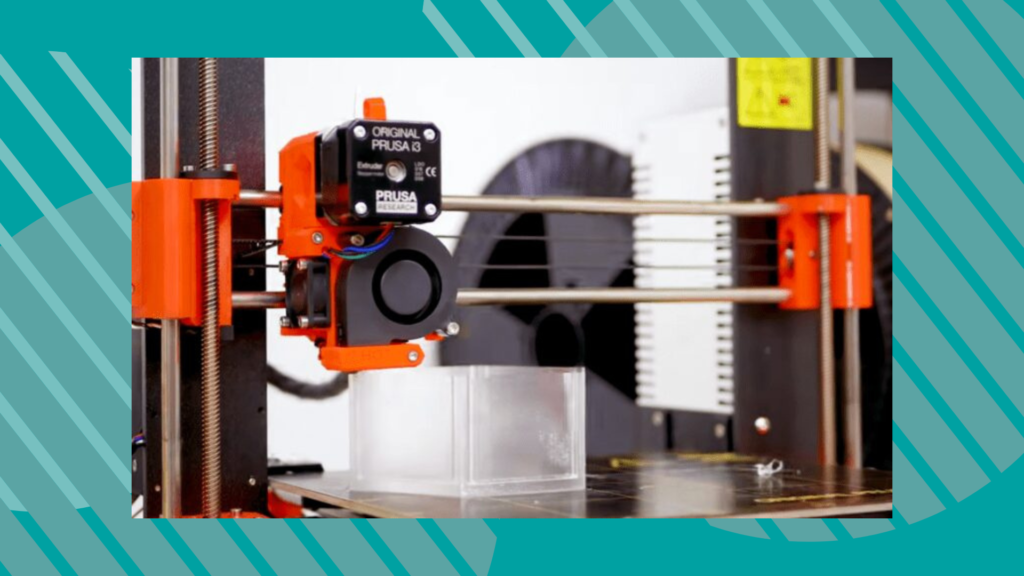
A Colorfabb utiliza seu filamento HT para essas impressões, que é o plástico Tritan, da Eastman. É, possivelmente, o mesmo material que a Taulman fazia, simplesmente chamado Tritan também. Mas o ponto chave aqui é que o material utilizado é um CoPoliéster, portanto, próximo aos materiais PET e PETG. Em geral, esses plásticos se fundem muito bem entre si, então, eles formam uma peça sólida de material, ao invés de terem linhas de camada muito aparentes ao longo da impressão. Queríamos ver como o PETG comum se comportaria, então, fizemos experimentos com um filamento mais barato, o PETG da Das Filament. No entanto, qualquer outro filamento de poliéster deveria funcionar basicamente da mesma forma para o que vamos demonstrar.
Consideramos aqui dois casos de uso: no primeiro, verificamos impressões sólidas, como a Colorfabb mostra, que parecem ser um bloco único, com linhas de camada basicamente imperceptíveis tanto por dentro como por fora (utilizamos engrenagens e o tradicional modelo do barquinho). O outro caso é impressões ocas, somente com uma casca e sem preenchimento, além de espalhar a luz, no nosso caso em específico. A aplicação aqui considerada para essas impressões é difusão de luz de várias formas diferentes, o que acreditamos ter alcançado. Mas, comecemos com as partes sólidas.
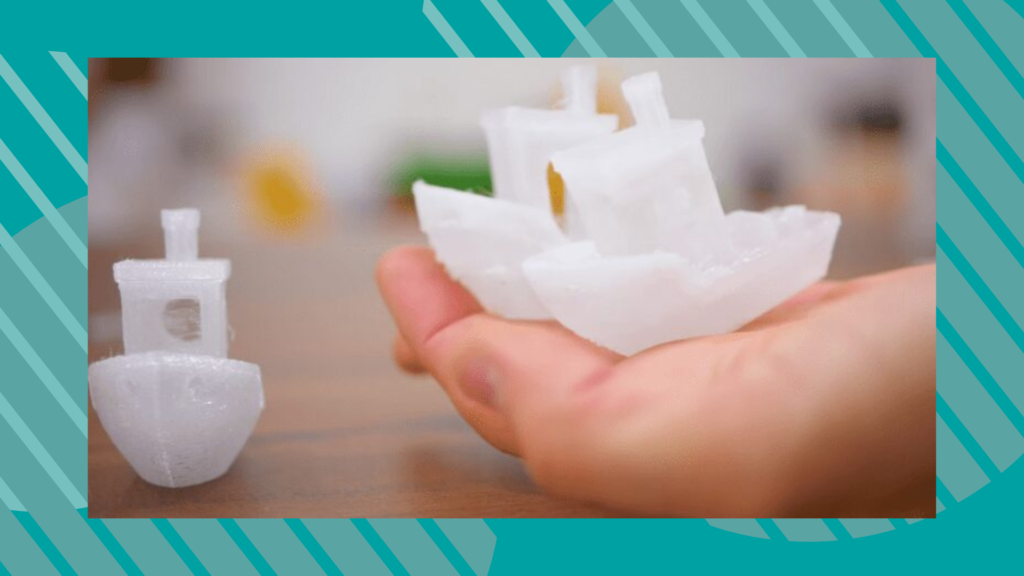
Nosso alvo de testes aqui é uma engrenagem do projeto OpenRC F1, de Daniel Norée. Ela foi escolhida por ter superfícies relativamente complexas nas laterais, grandes áreas planas no topo e no fundo e este encaixe, que é um elemento menor, por onde será possível ver a luz passar pelo topo e pelos lados. Obviamente, não é o design mais adequado quando o objetivo é fazer impressões esteticamente agradáveis, mas é um ótimo modelo para se ajustar um processo.
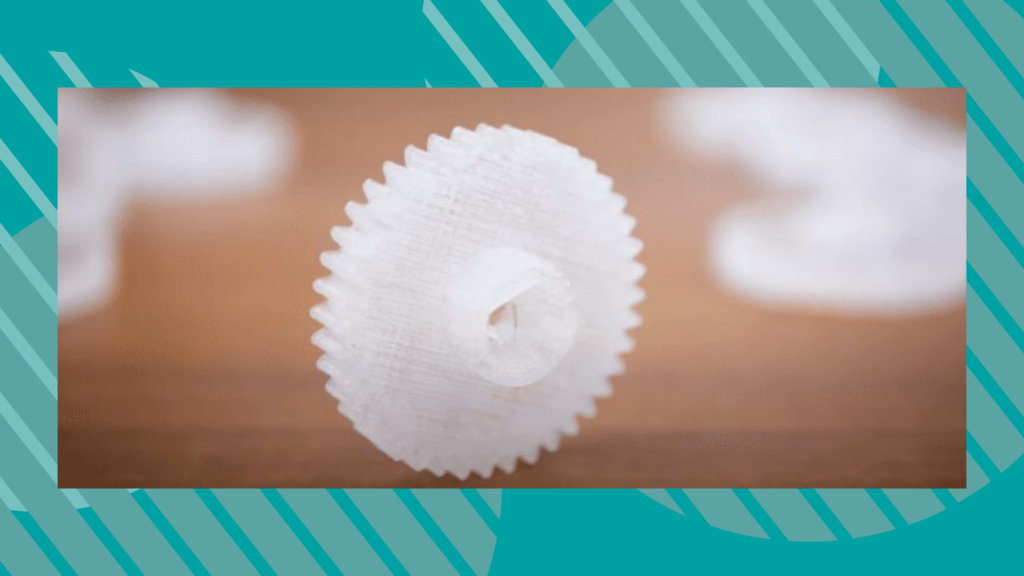
A primeira impressão foi feita com configurações que entendemos que faria sentido. Utilizamos camadas de 300um e 350um, 100% de infill e temperatura padrão. Porém, se olharmos para as peças impressas com essas configurações, elas são translúcidas, e não transparentes. Você pode iluminar a peça com a lanterna do celular, e ela vai deixar a luz passar, mas não é nem de longe transparente como as peças mostradas no artigo da Colorfabb. A primeira ideia foi aumentar o flow (volume de material que sai pelo extrusor por unidade de tempo, ou fluxo). Isso funcionou até certo ponto, fechando espaços que ficavam entre as linhas de extrusão num mesmo plano. Aumentamos a extrusão para 105% e, vendo que isso tornou o resultado um pouco melhor, aumentamos novamente para 110%. Se compararmos a peça original com essas duas impressões, vemos que já é bem mais transparente, apesar de mostrar também alguma sobrextrusão na camada do topo. Até aqui, parece que a quantidade de material está preenchendo os espaços corretamente.
Testamos, então, o outro extremo, utilizando camadass de 50um, o que imediatamente já ajudou no resultado. Possivelmente isso ocorre porque o bico de extrusão, que é quente, passa mais frequentemente sobre as partes já depositadas. Dessa forma, ele refunde as camadas de extrusão, levando a uma peça mais próxima a um bloco sólido de material. Por exemplo, veja essa peça quebrada ao meio: o interior da peça parece bastante ser PETG maciço. De fato, olhando-se somente a seção quebrada, é até difícil dizer que a peça foi feita por impressão 3D.
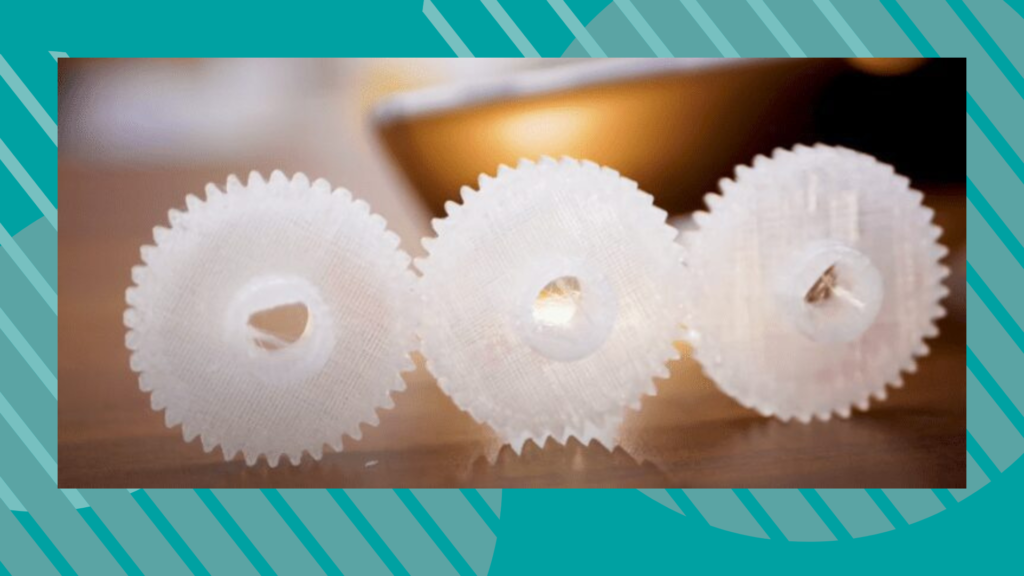
Então, começamos a aumentar o flow nas impressões de 50um e a aumentar a espessura de camada, de 50um para 100um. Nossa impressão foi que ambas as alterações melhoraram a transparência das peças. A impressão de 100um foi feita com maior perímetro, o que permite ver como a luz é espalhada de forma diferente dos cruzamentos que ocorrem no caso do infill 100%. No entanto, o resultado da peça, e geral, não foi muito diferente do da peça de 50um, a não ser pela superfície do topo, um pouco menos suave. Além disso, parece que houve nela um pouco mais de sobrextrusão.
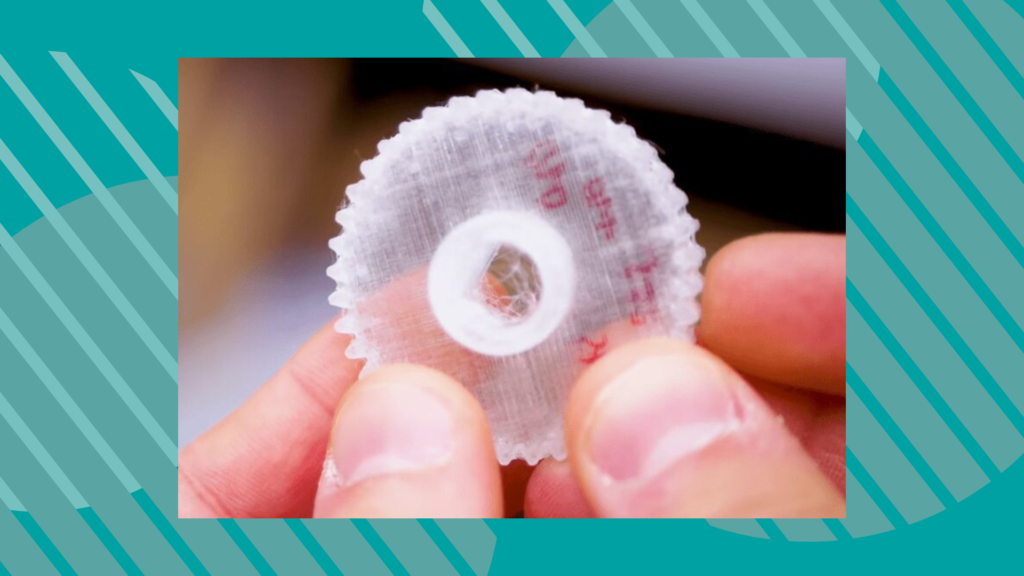
As peças de 50um com mais material foram, na nossa percepção, as amostras de melhor resultado, dentre a série de amostras que verificamos até aqui. A peça com 15% mais material ficou com uma transparência muito boa, enquanto a com 20% (acabamos por imprimir também com esse valor de sobrextrusão) mostrou que essa quantidade de material é exagerada, apresentando imperfeições no topo. Ela também apresenta locais onde o bico de extrusão acabou por esbarrar nas camadas depositadas, inserindo mais imperfeições. A princípio, pensamos que as impressões de 100um eram tão boas quanto as de 50um, e continuamos imprimindo peças com essa espessura. No entanto, concluímos depois que pode ser que tivéssemos melhores resultados se as tivéssemos impresso com 50um.
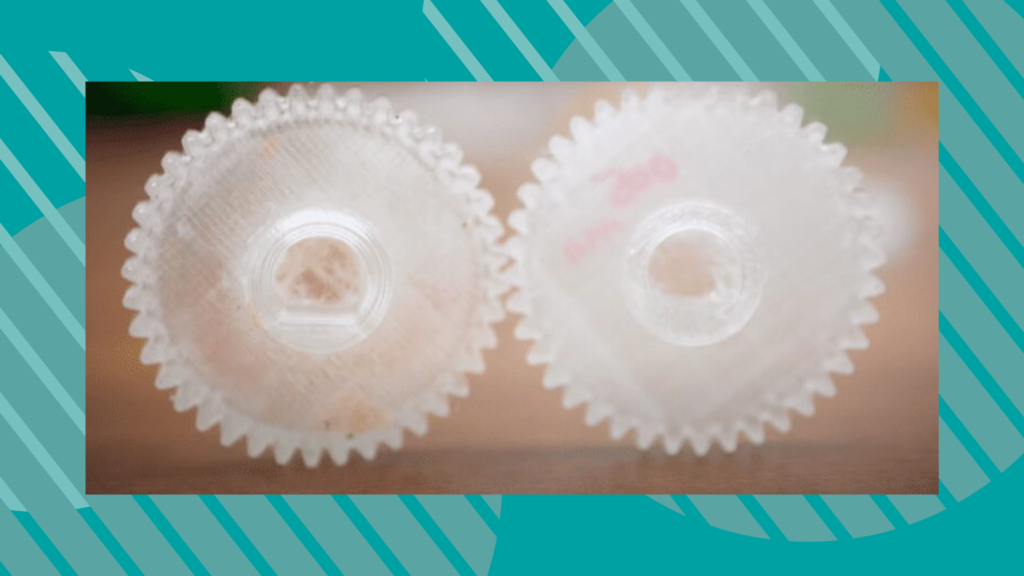
Prosseguindo, as duas peças a seguir foram impressas com flow rate de 110%, mas usamos um aumento de temperatura na primeira, esperando que isso ajudasse na fusão entre camadas. No entanto, o aumento da temperatura, na verdade, diminuiu a transparência da peça, além de alguns efeitos negativos adicionais na qualidade. É relativamente fácil de se ver o que acontece nas engrenagens em que utilizamos diferentes temperaturas: em temperaturas mais altas, o PETG começou a cozinhar e borbulhar, efeito que veremos novamente em breve. Nas partes periféricas das engranagens, a temperatura mais alta melhora levemente a transparência. No centro, porém, onde o bico de extrusão se de desloca mais lentamente (e a impressora diminui o fluxo para não depositar material demais num determinado ponto), nota-se que a aparência do material fica bastante esbranquiçada. Isso ocorre porque, quando a impressora diminui a velocidade do bico, o filamento fica exposto por mais tempo à área aquecida do bico, e, portanto, se aquece mais, cozinha e acaba por se degradar. Para evitar isso, no slicer, você pode escolher entre desabilitar o resfriamento em desaceleração ou, simplesmente, diminuir a temperatura de extrusão para todo o processo. No fim das contas, não faz muita diferença.
Esse barquinho nos parece muito bom no geral. Ele mostra a transparência, ou a translucidez, se preferir, muito bem. Ela é visível principalmente quando se olha o fundo ou o topo da peça, já que é quase como se a altura das camadas de baixo torna as superfícies nas laterais um pouco leitosas. Talvez fosse interessante tentar com uma altura de camada ainda menor, como 10um, mas acreditamos que a impressora utilizada (Prusa i3 MK2) não é capaz de suportar essa configuração sem a utilização de um novo extrusor e fuso do eixo z de maior precisão, já que a impressora possui resolução de 20um, considerando-se que a posição de meio passo do motor é a única variável desse grau de precisão em que você pode, de fato, confiar. Mas, voltemos aos testes com as peças!

Procuramos também melhorar o acabamento das superfícies utilizando polimento a quente, com o canhão de ar quente a 600 graus, ou lixando-as antes. Mas, com o canhão de ar quente, o spinner (imprimimos um fidget spinner para essa verificação) começou a borbulhar e amolecer antes de ficar mais transparente, então, perdemos essa peça. E, quando tentamos lixar a peça antes do aquecimento, com lixa 1200, ela de fato parece ter ficado mais transparente após a aplicação do ar quente. O que notamos é que pode ser bastante difícil achar esse ponto ótimo, onde o plástico não borbulha e nem se amolece demais.
Porém, algo que você pode fazer para qualquer tipo de filamento utilizando canhão de ar quente é remover as finas fibras que podem sobrar do processo de impressão (o que acontece especialmente no caso do PETG), enquanto o bico de extrusão passa rapidamente de um ponto do plano xy a outro. Uma única aplicação de ar quente é, normalmente, suficiente para se ver livre dessas fibras.
E, uma última abordagem, que acabou por não funcionar para um dos testes que fizemos no barquinho, foram a utilização de camadas mais grossas, de 300um. Mesmo com o multiplicador de extrusão aumentado, a peça não ficou nem um pouco mais transparente. No entanto, a qualidade de impressão se mostrou mais consistente se comparada às impressões com baixas espessuras de camada.
Portanto, recapitulando: com filamentos de poliéster, utilize baixa espessura de camada, 100% de infill, obviamente, e ajuste o multiplicador de extrusão para que você obtenha somente um pouco de sobrextrusão. Altas temperaturas podem ajudar, mas é bem fácil de se cozinhar o filamento utilizando essa abordagem. Com relação a pós-processamento, é bastante difícil de se fazer corretamente, pelo menos com ar quente. Talvez processos de recobertura de superfície com materiais apropriados podem ajudar, mas, neste caso, não melhoraram nada a transparência das impressões, com os testes que fizemos.
As próximas impressões que vamos analisar são as impressões sem preenchimento. A maior parte delas, você pode imprimir no modo base, que é um modo de impressão em que a peça é toda construída somente com uma única e longa extrusão, que se espirala para cima, ao invés de imprimir a peça em várias camadas. No entanto, as impressões sem preenchimento que possuem bordas bem destacadas normalmente não podem ser impressas com o modo base.
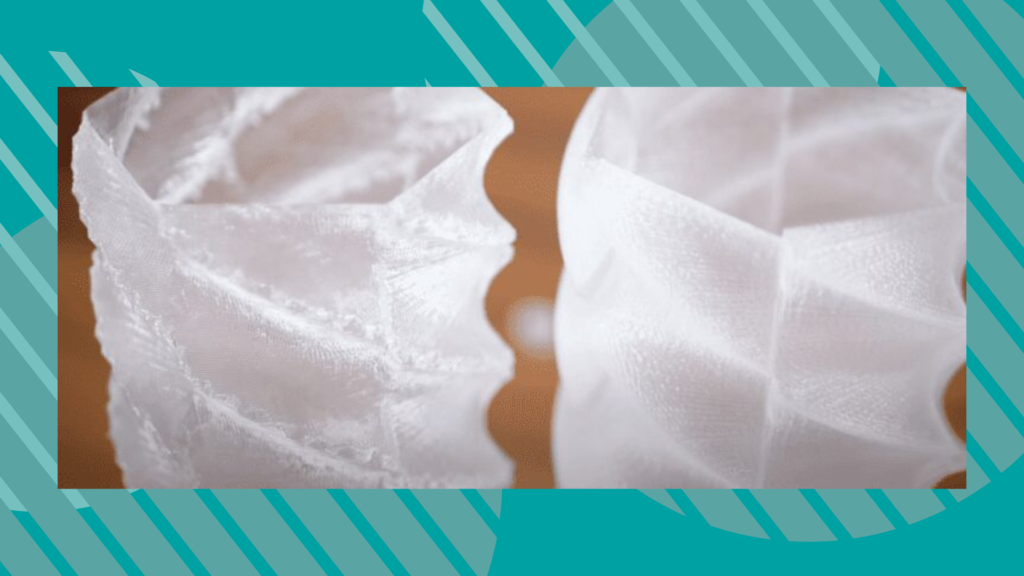
Comecemos com o que pode fazer com que essas peças fiquem melhores ou piores do que outras. Essencialmente, é a mesma coisa que já vimos. Os efeitos se devem à refração, que ocorre quando a luz passa de um meio para outro. Neste caso, é do ar para o plástico, e dali para o ar novamente. As camadas agem como pequenas lentes, pois elas têm laterais curvas. É por isso que esta peça, por exemplo, distorce a imagem na direção vertical, mas não tanto na direção horizontal. Por exemplo, com esta peça, tentamos utilizar esse efeio, criando microlentes, que difundiriam a luz também horizontalmente (a ideia da peça é ser um difusor de luz para uma luminária de fita de LEDs). Afinal, os pequenos LEDs individualmente não formam uma luminária bonita, portanto, criamos essas peças para provocar padrões diversos de difusão de luz. A maior parte deles foi impressa com espessura de camada de 300um, pois se você comparar com as que imprimimos com 100um, elas são muito mais transparentes e definidas, e têm menor presença do aspecto branco-leitoso.
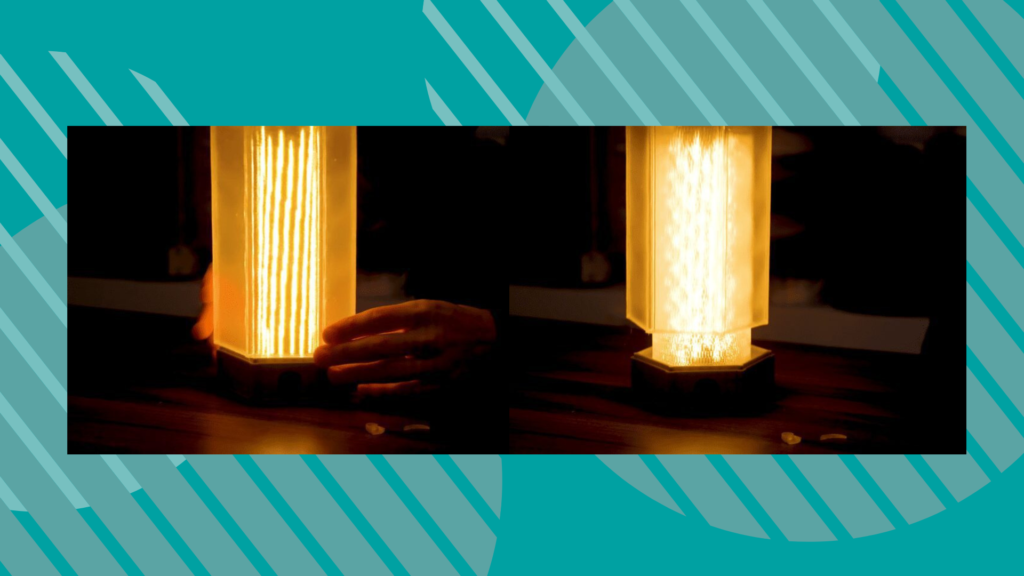
É claro que, utilizando uma espessura de camada grande numa impressão que é somente uma casca fina, as peças são impressas de forma incrivelmente rápida, utilizando pouquíssimo material. Esta, por exemplo, foi impressa com somente 25g de PETG, e em 45 minutos, o que é difícil de ser superado.
Este modelo, imprimimos com um diâmetro de extrusão um maior. Tipicamente, com um bico de 0,4mm, pode-se depositar trilhas de 0,42mm de diâmetro. Aqui, utilizamos 1mm. Ou seja, 2,5 vezes o diâmetro do bico. Essa abordagem não é a melhor se você tem grandes ângulos e detalhes, mas as peças para luminária sairam muito boas. Não fica tão transparente, mas isso pode ter ocorrido pelo fato de a estrutura da peça impressa com essa abordagem ser diferente. É, definitivamente, melhor do que imprimir perímetros 2D individuais, que introduz essa segunda interface, a qual pode acabar resultando em mais difração da luz. Além disso, a peça é bastante resistente e rígida, conforme esperávamos, mas o fundo foi rachado no processo de remoção da peça da cama de impressão. O PETG, comumente, se gruda com muita força na cama de impressão da Prusa i3, então, recomenda-se utilizar um acabamento líquido de superfície no topo da cama de impressão, que não se gruda da mesma forma (algo como Pintafix, Magigoo, ou até mesmo cola em bastão, se você conseguir aplicar uniformemente).
Porém, essa técnica de se utilizar uma única trilha de extrusão não é a melhor para qualquer modelo. Este modelo de dragão sai na impressão de uma forma muito bonita, mas sempre que houver uma inclinação significativa na superfície, as linhas de extrusão tenderão a se agrupar, como nas costas, próximo à cauda ou nas asas. Nós configuramos essa impressão com duas camadas sólidas, no topo e no fundo, e desativamos configurações que fariam o backfill de superfícies (o que eliminaria esses problemas, mas acabariam por criar estruturas internas que comprometeriam o nosso objetivo, que é obter uma boa transparência). Alternativamente, poderíamos ter escolhido imprimir com infill e camadas finas, mas isso levaria a um uso de muito mais material e levaria um tempo muito longo para terminar.
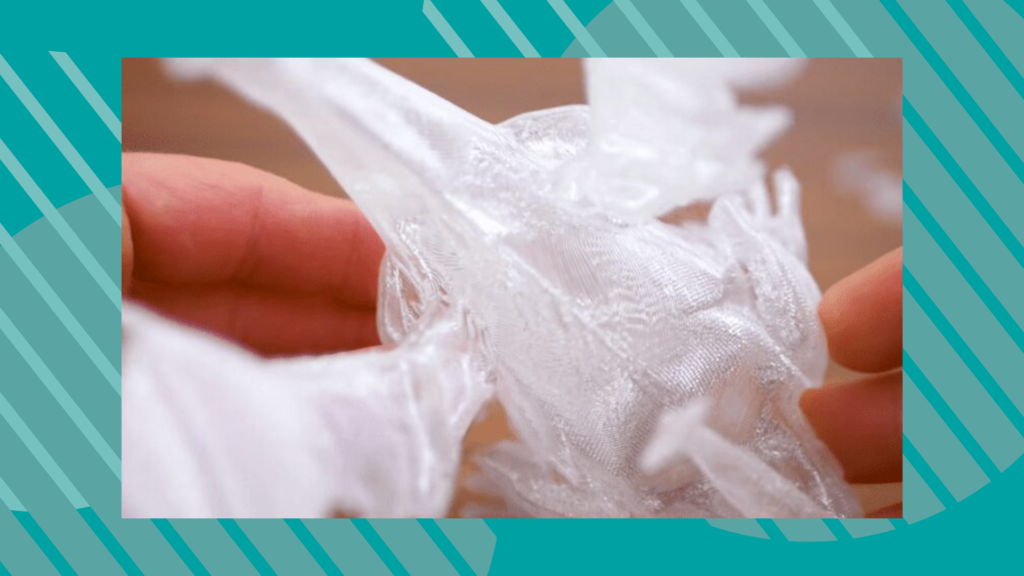
Camadas lentas, quentes e grandes
Outra informação importante é que quando deseja realizar uma impressão 3D transparente, é recomendável utilizar o filamento na sua temperatura máxima permitida. Alguns detalhes podem ser perdidos com essa característica mas, com certeza a impressão 3D transparente irá ganhar mais com a suavidade e garantirá uma melhor passagem de luz pelo objeto.
Parada para um detalhe técnico: para o filamento ABS, quanto maior a temperatura mais leitoso ele fica. Para o filamento PETG XT e o filamento TRITAN HT, quanto maior a temperatura, mais transparente ele fica!
A velocidade de impressão também deve ser um pouco menor do que o de costume e a impressora 3D em si deve estar muito bem configurada. Quanto melhor a configuração da impressora 3D, melhor a impressão 3D de fato e consequentemente a qualidade da impressão 3D transparente.
As camadas também devem ser grandes para diminuir a necessidade de mais delas e melhorar a passagem de luz pela peça.
Saiba mais!
A impressão 3D transparente é um desafio que requer atenção, a menor alteração na temperatura do bico extrusor, da velocidade de impressão e no resfriamento da peça podem afetar o resultado da impressão final. Felizmente existem alguns métodos de sucesso e é essencial saber que podem existir variações entre os materiais e os métodos de acabamento final.
E você, sabe como deixar uma impressão 3D transparente ainda mais transparente? Adoraríamos ouvir a sua experiência com impressão 3D transparente, conte-nos na sessão de comentários abaixo!
Portanto, foi assim que imprimimos peças transparentes/translúcidas. Em nossa avaliação, elas sairam muito boas, especialmente as impressões de extrusão única. Elas ficam muito bonitas quando utilizadas como luminárias. E, por este artigo, é tudo, pessoal! Esperamos que tenham aprendido algo com esses experimentos. Um abraço e até o próximo artigo!
Melhor coisa é imprimir em resina transparente, depois limpar com Vidrex ao invés de A. Isopropílico e passar verniz brilhante antes de curar. Assim ela não fica fosca
Melhor coisa é imprimir em resina transparente, depois limpar com Vidrex ao invés de A. Isopropílico e passar verniz brilhante antes de curar. Assim ela não fica fosca